绿色低碳发展优秀实践案例:以智能化数字化绿色化改造为引擎推动企业绿色低碳转型
2024-08-1310
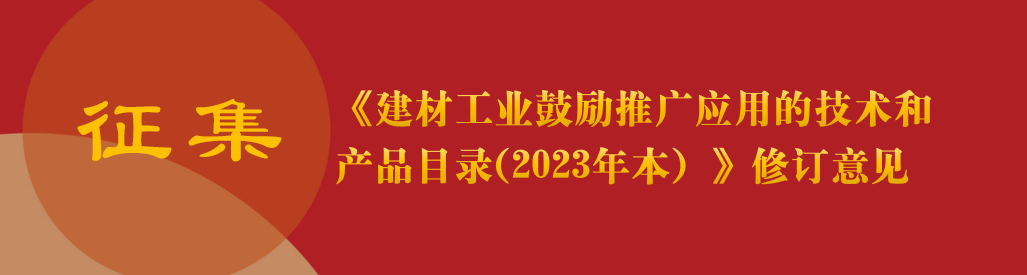
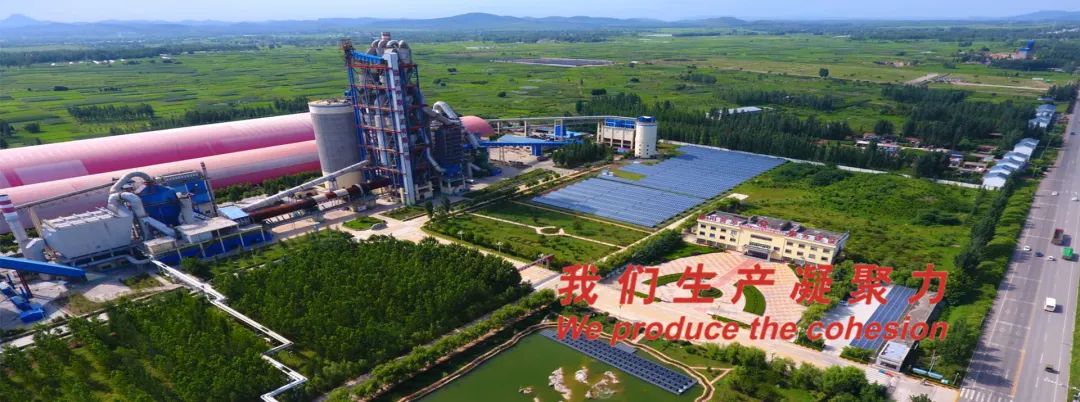
临沂中联水泥有限公司成立于2004年,公司注册资本1.652亿元,固定资产17.6亿元,厂区占地总面积1027亩。公司位于临沂市兰陵县车辋镇,公司主营业务为水泥产品的生产研发和销售。公司主要产品为复合硅酸盐水泥、普通硅酸盐水泥、低碱水泥、缓凝水泥等。
该公司始终坚持“绿水青山就是金山银山”的发展理念,秉承中国建材集团“善用资源、服务建设”的核心理念,把该公司打造成“创新绩效型、资源节约型、环境友好型、社会责任型”四型企业。
(一)设备智能化
1.质量管理智能化
在生料质量控制方面,安装赛默飞世尔生料在线分析仪,有效保证了回转窑热工制度,促进熟料烧成煤耗降低,达到节能减碳效果。
在水泥质量控制方面,引进英国马尔文在线粒度分析仪,实现出磨水泥细度实时在线检测,避免人工取样检测不连续、检测结果滞后等问题,使水泥质量更优,能耗更低。
在原材料和产成品化验方面,安装荷兰帕那科荧光分析仪,同时引进MLD检测法,使用熔片法通过荧光分析仪检验物料的化学成分,较人工滴定法效率提高70%。
在设备在线监测方面,安装设备智能在线监测系统,实现设备的预检预修管理。在电机管理方面,引进电机健康管理系统,为设备管理人员提供可视化的画面,提前发现设备隐患,实现电机预检预修管理。在智能控制方面,安装ABB DCS控制系统,替代原有的国产DCS系统。通过建立算法模型,云端处理数据,实现自动控制生产操作,使生产系统时刻运行在最优状态,实现高质高效生产,减少污染物排放。进行四代中置辊破篦冷机改造,冷却面积由122m2提高到160m2。回转窑产量由技改前5595t/d提高到5840t/d,二、三次风温提高80℃,出篦冷机熟料温度至环境温度+65℃以内,熟料,3d抗压强度提高1.6MPa,28d抗压强度提高1.2MPa。技改后,窑尾收尘器压差由3200Pa降低为2100Pa,收尘器出入口温差由30℃以上降低为8℃,窑尾烟囱氧含量降低1.3%,窑尾排风机转速降低1HZ,平均运行功率降低280KW,出生料磨负压提高800-1000Pa,窑尾电耗降低2.1kwh/t熟料。煤磨通风机进行改造,安装新型涡轮高效节能风机。改造后风机效率提高到80%以上,高温风机功率由2200KW降为1800KW,煤磨通风机风机功率由320kW降低为240kW,每年可节约用电量240万度。技改后装机功率为459.5KW,技改后每小时节约用电量130度,每年节约用电量65.5万度。技改为永磁电机,改造后节电量为15%,每年可节约用电48万度。对高温风机、水泥磨循环风机、篦冷机三段风机等进行变频改造,改造后启动电流降低30%,运行过程节能效果明显。预热器结皮厚度较技改前降低90%,由此带来通风条件大大优于改造前;由于结皮量的降低,基本消除了因厚结皮产生的工艺事故;系统结皮降低,稳定了系统煅烧工况,稳定产品质量。配合煤粉燃烧器,质量提升6%,估算对提高产质量产生的效益约60万元/年。技改为四支新型旋流扩散型分解炉燃烧器。燃烧器能保证煤粉喷射的旋流扩散效果,使煤粉迅速扩散,均匀混合。对现有撒料箱进行技改,由固定式撒料箱技改为可调节式撒料箱。保证在煤粉起燃后与生料混合均匀,保证不塌料。技改后氨水用量较技改前降低20%,氮氧化物排放量可以达到50mg/m3以下。利用空闲土地修建4000m3污水处理池,余热发电冷却污水、制水设备废水全部回收利用,用于立磨喷水、洗车机用水、道路洒水、喷淋,料棚喷水等,减少新鲜水消耗。通过以上措施,该厂重复用水率达到90%以上。该厂利用回转窑建设余热发电系统,大大减少了传统煤电消耗,年减少碳排放4万余吨。利用风力和太阳能资源,年可节约用电36万kWh。该厂建设云数据中心,为该厂数字化转型提供了基础条件。云端赋能工业互联网和打造“智慧”工厂,构建了以业务数据和业务应用为核心的新一代企业级IT基础设施平台和应用平台,使每年的运维成本至少节约30%。该厂建设基于私有云模式的水泥生产全过程智能管控平台,实现数字化,消除信息孤岛。该厂持续加大工业废渣综合利用和危废处置力度,消纳社会垃圾,年可节约原煤消耗9000吨,减少碳排放1.98万吨。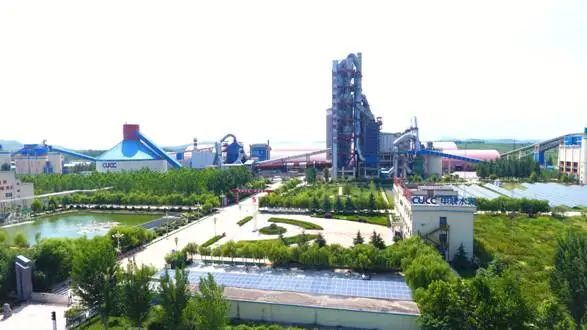
该厂通过开展绿色低碳改造项目,智能化和数字化水平进一步提高,打造了基于私有云模式的水泥生产全过程智能管控平台,形成大数据中心,发掘了数据背后的价值,并将分析结果用于指导管理改进,提升决策效率,实现更加精准与透明的企业管理,实现供应链管理优化、生产管控一体化、企业决策管理数字化,推动企业高质量发展。项目开展后,该厂计划达成率提高4.6%,生产效率提高21.1%,产品产量提高15%,降低能源消耗1.88万tce/年,降低碳排放量5.3万吨/年,产品质量提升5.5%以上。由于对设备的监控手段更为先进和有效,设备运维成本降低15%,年节约维修费用50万元,综合计算每年为企业创造效益750余万元。编辑:段丹丹
审核:东朝莉、王玉敏
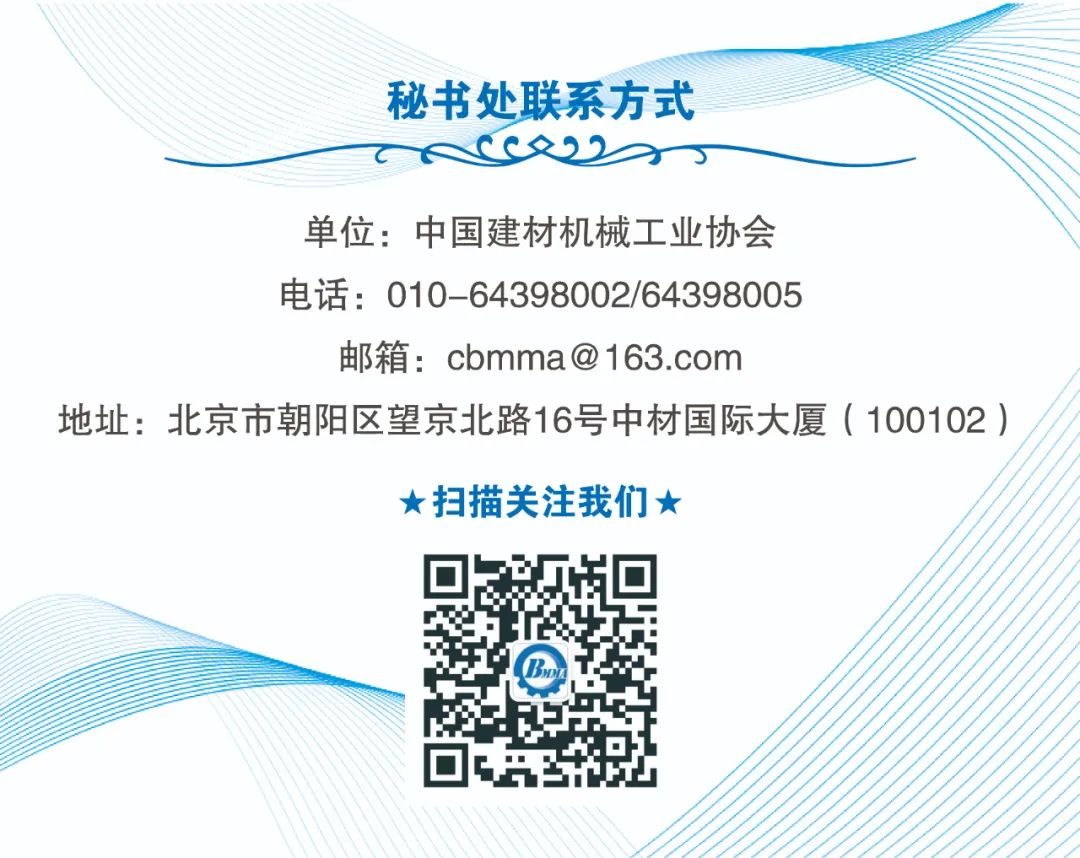
点我访问原文链接